
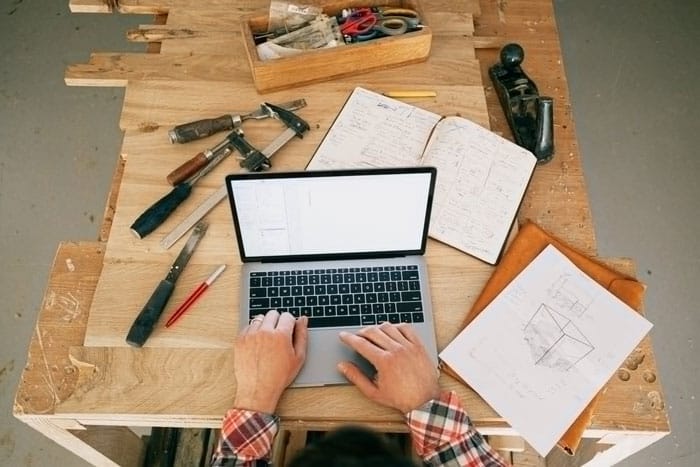
Your production scheduling will help with demand planning, supply, and the changing needs of your customers. The benefits of using a production schedule Production quantities (the number of units you’ll produce each week).A variation sublist (size, color, type).A product inventory that lists all of the products you make.Your production schedule will include these elements: What to include in your production scheduling Maintenance: Keep your schedule updated regularly as demand changes.Execution: This is the process of putting your plan into action.Dispatching: Plot the process of items and people moving around - including when and where throughout the entire process.Communicating: Share the production schedule to everyone involved and make sure it’s understood.– Plan a retail schedule that covers how products move from manufacturing to the shelf or eCommerce store
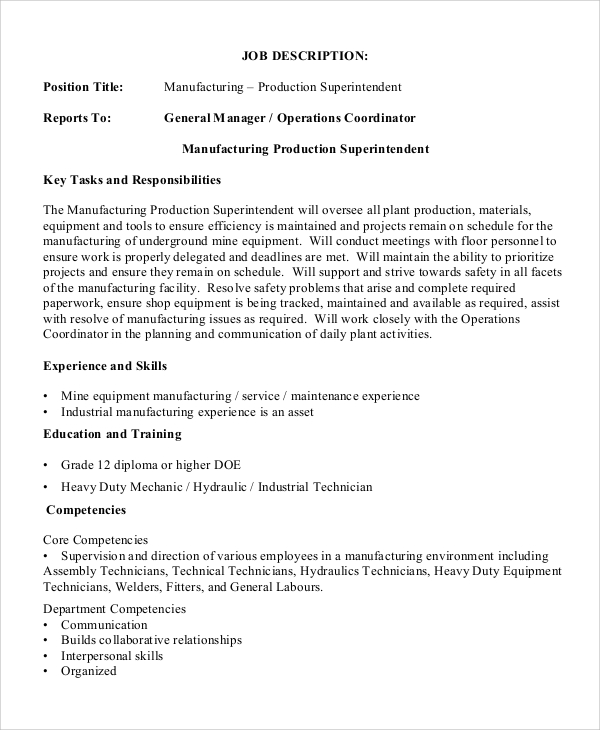
– Set up a manufacturing schedule that covers raw material routing – Create a master schedule that encompasses the entire process, from start to finish
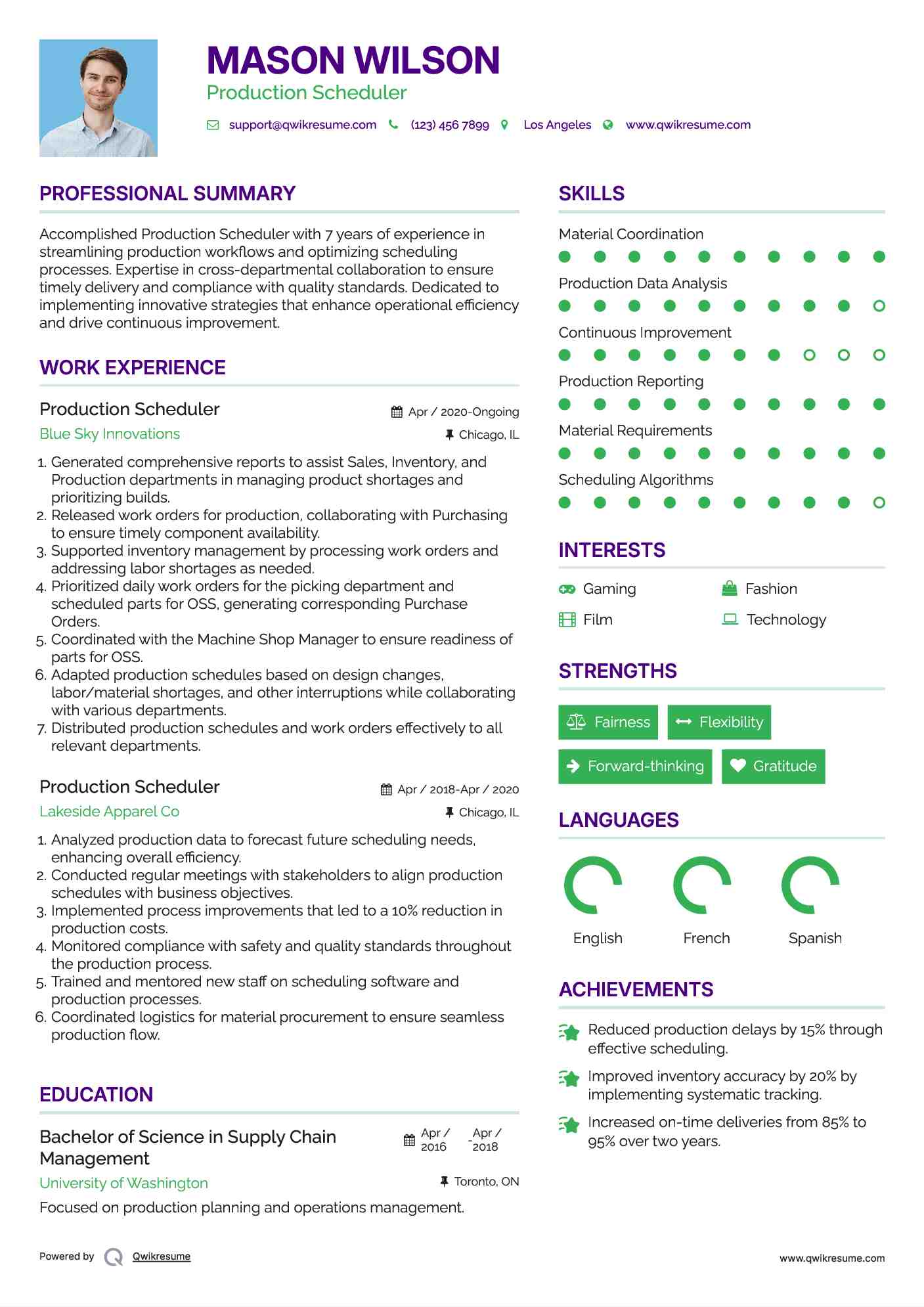
Static assumes nothing will change, whereas dynamic assumes everything could change. How much raw material will you need, and when? There are two types of planning you can do here: static and dynamic.
#Scheduler job description manufacturing how to#
Improved communication: With one master document detailing every element of the production workflow, communication is standard across the entire business How to create a production scheduling process This results in improved lead times and smoother demand flows Improved efficiency: Spotting bottlenecks and looking for areas of improvement. Stockout prevention: Planning to maintain output, even if materials are delayed, or a swell in orders increases demand Scheduling: Assigning workers and detailing contingency plans for when unexpected delays happen Planning: Predicting demand and matching that to labor, materials, and equipment capacity Let’s get into its main functions in a little more detail. It helps keep your operations working on time and under budget, which helps you keep your commitment to your customers. The production schedule is a versatile and important document for planning, forecasting, predicting, and meeting demand. Manufacturers then tell sales when the product is ready. Sales inform the manufacturing team about the levels of demand.
#Scheduler job description manufacturing update#
For this reason, it’s a flexible, changeable document that you’ll need to update and check regularly.Īs well as helping managers plan ahead, the production schedule works as a line of communication between production and sales teams. It also incorporates various processes designed to make production run smoothly while helping managers spot potential issues - like bottlenecks - and stop them before they explode into something bigger. It includes every detail, from raw materials to logistics. Read on to find out more! What is production scheduling?Ī production schedule lists every single product that’ll be manufactured, including where and when they’ll be made. It’s a handy process that helps your business meet customer demand more efficiently. It’s nearly impossible to predict an event like COVID-19, but for everything else, there’s production scheduling. When you do see empty shelves, it’s usually because someone has struggled with procuring materials, work orders - or there’s been a natural disaster or pandemic. We’re so used to going to the store and seeing the stuff we need in abundance because, over time, manufacturers have gotten very good at getting the right materials in, manufacturing on time, anticipating demand, and shipping it off to the store. There’s absolutely no way manufacturers could’ve predicted this once-in-a-lifetime combination of events, and the result was… we ran out. Remember the great toilet paper panic of 2020? Hundreds of thousands of people rushed out and stockpiled what became, for a few months, one of America’s most sought-after commodities.
